Vietnamese Traditional Bamboo and Rattan Weaving Production Process: From Raw Materials to Completion
- Admin
- Mar 12
- 2 min read
Updated: Mar 25
Traditional bamboo and rattan weaving has become one of the unique cultural features of Vietnam, carrying the essence and heritage of the nation. The production process of traditional bamboo and rattan weaving not only requires skill and dedication but also emphasizes meticulous craftsmanship in every stage. Let's explore the traditional bamboo and rattan weaving process with GreenWeaver to understand the secrets behind these artistic creations and the cultural value of this traditional handicraft.

Step 1: Selecting Bamboo and Rattan Materials
Choosing the right materials is the most crucial step in the production process, as it directly affects the quality of the final product.

The best bamboo must not be too young or too old, should grow straight, and have high hardness.
Similarly, high-quality rattan must be of moderate thickness, about 5 meters long, straight, uniform, and free from diseases.
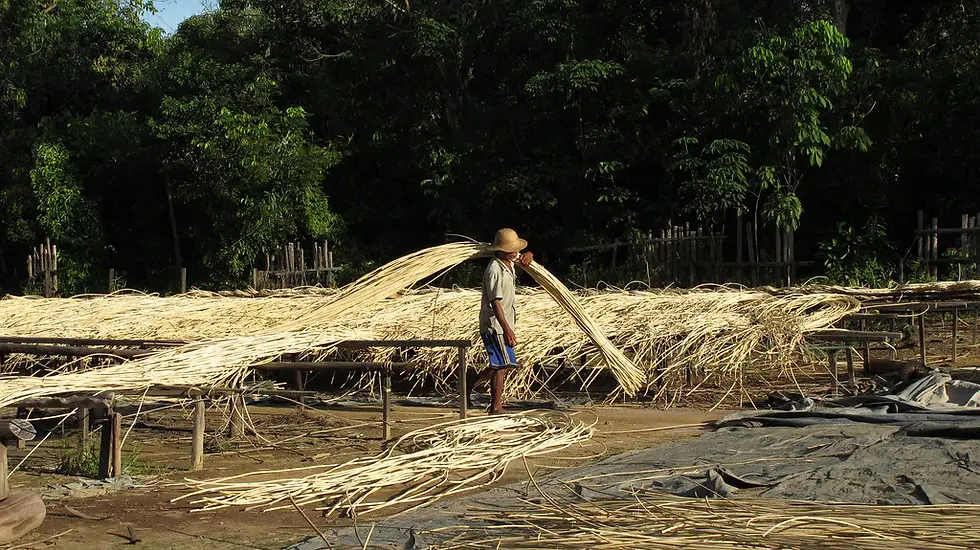
Overaged or underdeveloped materials are not suitable for production.
Step 2: Initial Processing of Materials
After selecting the raw materials, they must undergo initial processing to remove impurities and ensure cleanliness. This step is essential to prevent termites, mold, and extend the lifespan of the final product.
Bamboo processing: Bamboo is cut into sections and dried. It is then treated to prevent termite infestation and ensure durability.
Rattan processing: The outer thorny layer of rattan is removed, exposing the smooth inner surface. It is then dried to prepare for the next processing steps. This process helps clean the rattan and maintain its natural color.

Step 3: Material Treatment
Before use, the materials need to be treated to create a smooth and durable surface for the final product.
Bamboo treatment: Bamboo is peeled, then placed in a kiln for smoking and drying. This process softens the bamboo and enhances its color stability.
Rattan treatment: Rattan is also processed to ensure a smooth, glossy surface. It is dried to preserve its natural hue. This step requires careful attention and skilled craftsmanship.

Step 4: Splitting the Fibers
Splitting the fibers is a crucial and time-consuming step in the bamboo and rattan weaving process. Both bamboo and rattan must be split into thin strands to be woven into various products. This enhances the flexibility of the material, making it suitable for different designs. The size and length of the fibers depend on the specific product being crafted.

Step 5: Crafting Bamboo and Rattan Products
Once the fibers are ready, artisans begin crafting the bamboo and rattan products. This process includes weaving, gluing, painting, and applying protective coatings. Fine details such as patterns and decorative elements are carefully refined to ensure precision and elegance.
This final stage is crucial in transforming raw materials into unique and exquisite traditional bamboo and rattan artworks.

The traditional rattan and bamboo weaving production process requires many stages and effort. Rattan and bamboo woven furniture products are sophisticated, unique and aesthetically applicable, in line with classic and modern trends.
Are you a home decor business owner looking to stock unique, high-quality, and eco-friendly handicrafts at unbeatable prices? Partner with GreenWeaver from Vietnam! Browse our collection and bring sustainable, beautifully crafted decor to your customers. https://www.greenweaverstore.com/all-products
Comments